*Dr. Samer Arnous, Coronary and structural Interventional Cardiologist, at University Hospital Limerick trying the visor on for size at UHL. Photograph: Sean Curtin (True Media).
100,000 face visors have been manufactured for HSE front-line staff as part of a collaboration between the University of Limerick and UL Hospitals Group.
A two week project has seen the design of solutions to critical clinical challenges facing healthcare professionals in the pandemic. With previous experience in rapid design and 3D printing of medical devices in response to clinical requests, the Rapid Innovation Unit at UL and SFI research centre, CONFIRM mobilised teams to innovate immediate solutions for COVID-19.
Potential shortages of equipment were identified should cases surge which prompted the request by Professor Paul Burke, Chief Academic Officer at UL Hospitals Group to the rapid innovation unit.
Protection of HSE front line staff will be enhanced plus treatment capacities will be increased as part of the measures, officials say. It follows the manufacturing of 100,000 face visors for front-line staff, refinement of a shield concept to protect anaesthesiologists during patient intubation for ventilation and design of adapters for respiratory technologies to undergo a clinical trial.
On Thursday, the first batch of visors were delivered, the shield box and adaptors are expected to be put into practice over the weekend. The face visors are in Limerick green and say ‘The Limerick Visor: Front Line Heroes’.
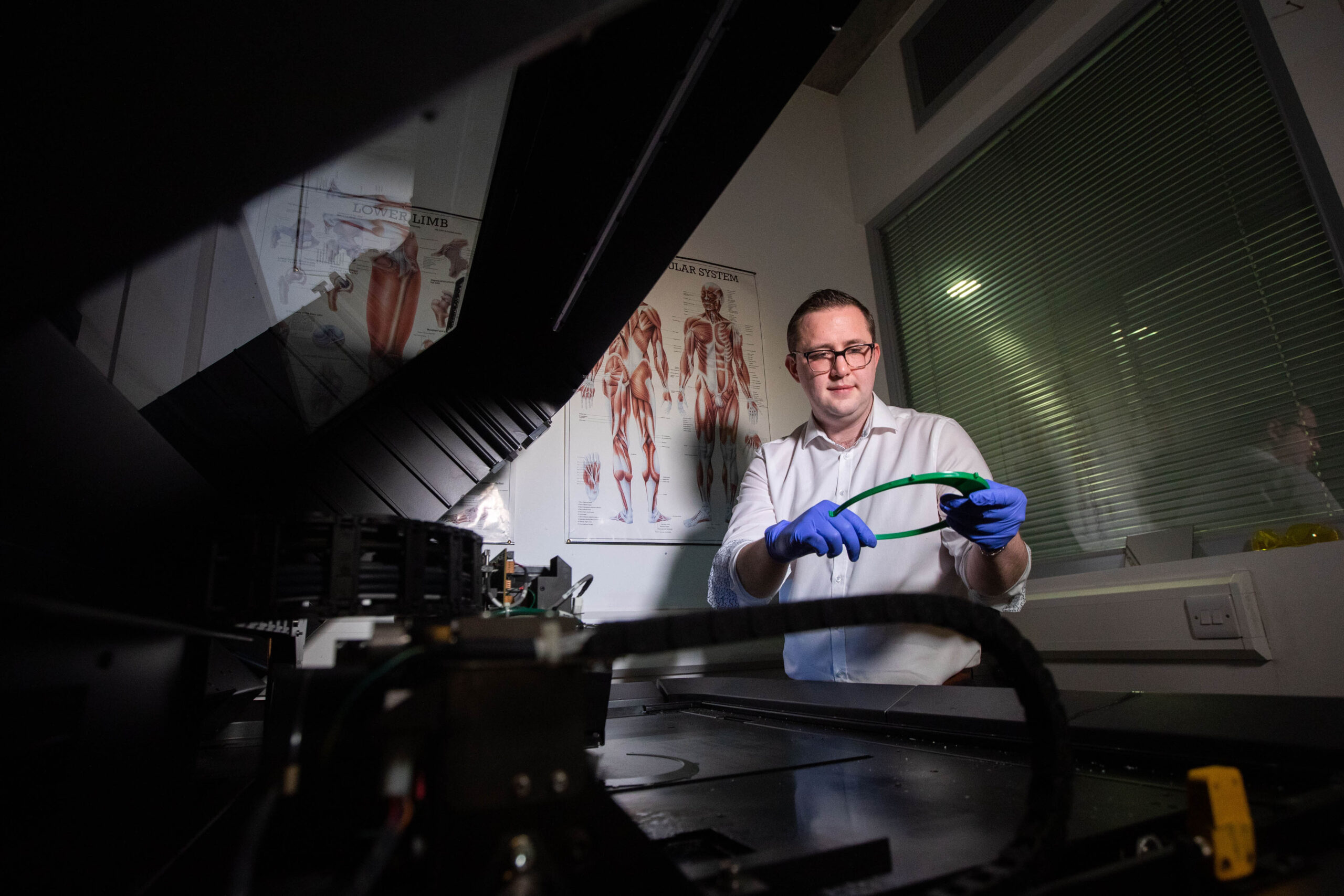
“There has been a phenomenal collaborative effort to deliver these solutions in a very short timeframe,” explained Professor Leonard O’Sullivan, of UL’s School of Design and the Health Research Institute based at UL. He noted that brothers Aidan and Kevin O’Sullivan, research fellows at UL, had “pulled out all the stops to lead the team to deliver these rapid response solutions for the hospital”.
Professor Paul Burke explained: “We have heard the World Health Organisation repeatedly stress the importance for governments, healthcare professionals, scientists and industry to act with speed in response to COVID-19”.
Regarding the face visors, Professor O’Sullivan explained the local companies had enabled capacity to manufacture up to 5,000 visors a day. “The visors can be for multiple use but it is likely also be for single use given the current circumstances,” he said.
The normal production time on a project like this would take months, but it was done in just nine days. This was accomplished through the local companies working very intensively together, Professor O’Sullivan highlighted. “We had a team of three consultants and three designers involved in daily brainstorming and design review meetings, which is something you don’t have except in a critical situations”.
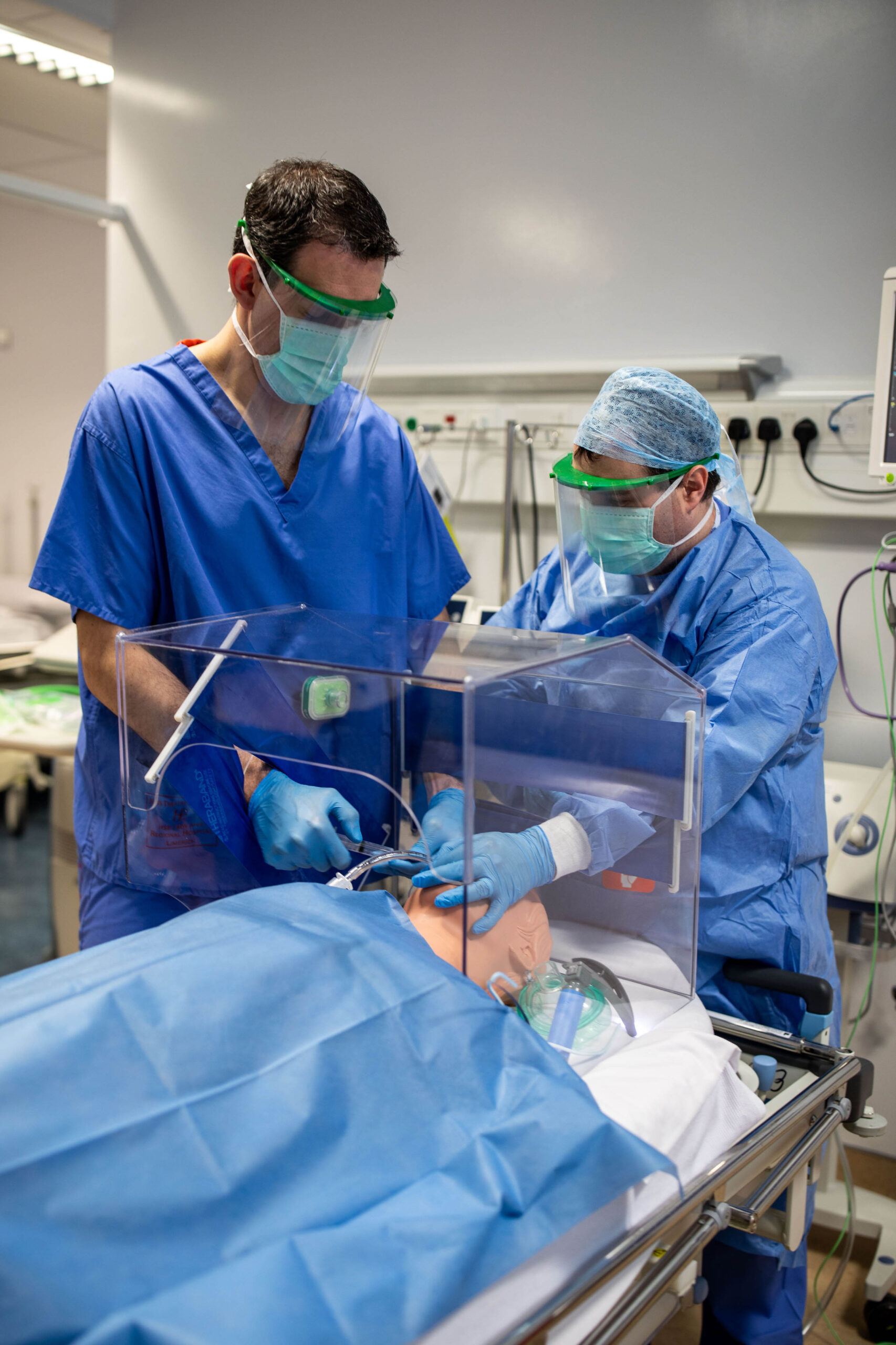
“We went to the coalface to establish what the critical needs were and we delivered solutions. This had to be done as quickly as possible. The local industry partners worked tirelessly to meet the volume production requests,” said Professor O’Sullivan.
Tony Moloney, Consultant Vascular Surgeon, UL Hospitals Group, said: “It seems like a long time ago but it was only on March 26 that the scientists and clinicians who form the Rapid Innovation Unit met for the first time on this. Everything we have ever done as a group has been done remotely in keeping with the COVID-19 guidelines”.